Maintenance of Press Brake in UAE
Maintenance of Press Brake in UAE Proper maintenance is important for ensuring the longevity and performance of a press brake machine. Here are some steps you can take to maintain your press brake machine:
TFICo. Press Brake Bending Machine top 5 benefits
TFICO Press brake bending machine top 5 benefits A press brake machine is a machine tool that is used to bend sheet metal and plate into various shapes and forms. Here are five benefits of using a press brake machine: Precision: Press brake machines are highly accurate and precise, which allows for the production of […]
Guillotine shearing machine Benefits
Guillotine Shearing machine Benefits A guillotine shearing machine, also known as a guillotine cutter or squaring shear, is a machine tool used for cutting sheet metal or plate. It consists of a blade, or upper beam, mounted on a frame that is driven by a motor or hydraulic system. The material to be cut is […]
Press Brake machine Benefits
Press brake machine benefits Press brake machines are widely used in the manufacturing industry for bending and forming metal sheets and plates. These machines offer several benefits that make them an essential tool for any metal fabrication shop. Here are five paragraphs about the benefits of using a press brake machine: Accuracy: Press brake machines […]
Qazvin- Bandsaw H1200
1 Model QAZVIN- H1200 2 Max. Cutting Capacity Round: Φ1200mm Plate : 1200x1300mm 3 Blade Speed From 12 up to 60m/min 4 Blade Size 11460x67x1.6mm 5 Vice Clamping Hydraulic 6 Blade Tensioning Form Manual 7 Feeding Out Adjust Way Hydraulic Stepless 8 Feeding Way Automatic 9 Main Motor 15Kw 10 Hydraulic Motor 2.2Kw 11 Coolant […]
TFI Co. Bandsaw Machine Qazvin-HDC600
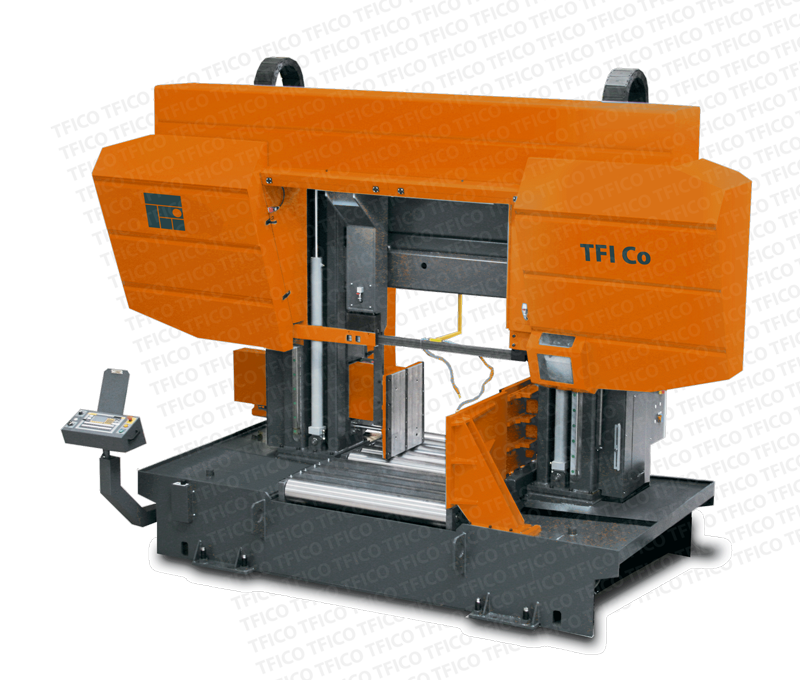
TFICO CNC HORIZONTAL DOUBLE COLUMN BAND SAWING MACHINEMANUFACTURING OF CNC HORIZONTAL DOUBLE COLUMN BAND SAWING QAZVIN MACHINETECHNICAL DATA : 1 Model QAZVIN- HDC600 2 Max. Cutting Capacity Round: Φ600mmPlate : 600x700mm 3 Blade Speed 20,37, 48, 66 m/min ( Stepless Speed) 4 Blade Size 6260x41x1.3mm 5 Vice Clamping Hydraulic 6 Blade Tensioning Form Manual 7 […]
TFICO HORIZONTAL BAND SAWING QAZVIN MACHINE Qazvin H1200
1 Model QAZVIN- H1200 2 Max. Cutting Capacity Round: Φ1200mmPlate : 1200x1300mm 3 Blade Speed From 12 up to 60m/min 4 Blade Size 11460x67x1.6mm 5 Vice Clamping Hydraulic 6 Blade Tensioning Form Manual 7 Feeding Out Adjust Way Hydraulic Stepless 8 Feeding Way Automatic 9 Main Motor 15Kw 10 Hydraulic Motor 2.2Kw 11 Coolant Pump […]